面料染整色差技术分析,形成面料色差的主要因素,染色面料色差的预防与控制
供应灯芯绒面料烧毛坯,承接灯芯绒染色成品订单!微信:13801503159
导致染色成品布产生色差的因素多且复杂,要将色差严格控制在标准范围之内且使其长期保持稳定,涉及到生产加工过程中的方方面面,必须对各个要素和影响因素进行综合分析,制定出相应的预防措施,严格规范实施手段,对染色织物的色差加以控制。
染色成品的色差一般分为:原样色差、前后色差、左中右色差和正反面色差(俗称阴阳面)四大类。原样色差是指染色织物与客户来样或标准色卡样,在色相、色光和色泽深度上存在的差异;前后色差是指相同工艺先后染出的织物在色相、色光与深度上存在的差异;左中右色差是指染色织物纬向左中右部分的色相、色光与色泽深度存在的差异;正反面色差(阴阳面)是指平纹织物两面的色相与色泽深度存在的差异。以下结合生产实践;简要分析产生这四类色差的原因;并提出预防和控制措施。
形成色差的主要因素
1、前处理
随着印染生产加工技术的进步与发展,前处理的处理能力、处理质量及处理效果对印染加工成品质量的影响越来越突出。业内专家认为,70%左右的产品质量应控制在前处理工序中。
在织物印染加工过程中,前处理后的半成品所存在的疵病一般都具有一定的隐蔽性,特别是对织物的内在质量指标有影响的疵病,很难判断查明。前处理中造成织物成品色差的影响因素主要有退浆除杂不匀、不净;前后、左中右毛效不一致;白度批差大;丝光不匀透;水洗效果差;半成品布面碱性过大等。
半成品退浆除杂不匀、不净
织物经过煮练、漂白工序后,色素已被除去,仅从织物布面很难发现其退浆及除杂不匀、不净的质量问题。用这种半成品生产漂白和浅色品种,容易产生泛黄、变色、色相不稳定(色萎、色暗)、艳度较差等问题;此外还会影响织物的丝光和染色效果,造成织物表面丝光和染色白芯等疵病。丝光时,织物出丝光机第一浓碱槽、进第一轧点前,若布面出现花斑,表明丝光时织物吸碱不均匀,这就是半成品退浆除杂不匀、不净的表现。这样的半成品在打底机轧染液时,还会发生吸色不匀现象。
半成品毛效、白度
我们平时所强调的织物半成品前处理效果好,并非只是讲退浆除杂净、毛效高、白度好,而是强调“匀”,也就是半成品质量的一致性和稳定性。在前处理加工过程中,设备状态、工艺条件及参数等因素的波动,都会影响织物半成品质量的一致性。例如,水洗轧车的左右压力差较大或轧辊凹心严重,会使织物两边、中间的水洗效果有较大差异,染色时则会因织物毛效、白度不一致,导致织物左中右色差。同样,轧料轧车的左右压差或凹心会造成织物两边、中间的轧余率不一致,使织物染色后出现色差。另外,药剂和助剂追加不稳定、水洗温度忽高忽低、车速忽快忽慢都会导致前处理半成品毛效、白度不一致,进而造成织物前后色差。特别是直接性高的染料,如活性、印地科素、纳夫妥等染料的染色,很容易产生色差,即使是直接性不太高的还原悬浮体、分散染料也会有明显的色差产生。这主要是因为毛效高的半成品吸湿性较好,上染率较高,得色较深;反之,毛效低的半成品吸湿性差,上染率低,得色浅,因此造成织物染色时上染不匀。需要强调的是,待染半成品白度不一致,也会对织物的色光造成很大的影响,在生产漂白和浅艳色染色品种时,尤为明显。
半成品丝光工序
丝光效果对棉纤维上染率的影响较大。丝光工艺条件及参数的不稳定,对织物染色的影响非常明显,如浓碱槽碱液浓度的大幅波动、生产加工过程中车速的忽快忽慢,都会影响棉纤维的丝光效果,并由此造成织物染色色差。另外,织物丝光落布pH值的不稳定,即丝光织物的去碱、水洗效果差或不稳定,也会对织物染色产生不良的影响。尤其在生产涤棉染色织物和用对碱较为敏感的染料染色时,pH值偏高或不稳定,会使织物染色后色光变化较大,造成色光萎暗、色相不稳定、明艳度较差,使织物产生原样色差。
2、染色
染色工序是织物染整加工的关键工序之一,也是织物色差体现较集中的工序,该工序对织物产生色差的影响因素较多,也较复杂。依据生产实践,大致可分为染料性能、染液配制、工艺条件和设备性能等四类主要影响因素。
染料性能
织物染色前首先要配色打样,打样时选择染料有两种基本方法:一是选择一只与所染色泽相近的染料,然后再添加少量其它染料对其色光进行调整;另一种方法是,用三原色拼色,这种方法能拼出大部分色泽,是染色布的主要选料方法之一,但所用染料种类太多,会影响织物的色泽、深度和鲜艳度。若织物染色后色光变化较大,就会造成织物的原样色差,即不符样。
有些染料具有热变性,即高温会造成染色织物的变色或色光变化。活性染料和士林染料受热变性较为明显,其恢复正常色光的时间很长,个别染料甚至需要十几个小时或更长的时间。如一般绿色染料受热时偏蓝光,受冷时偏黄光;而士林莲IR受热时偏红光,受冷时偏蓝光。这就会造成织物染色后的色光不稳定或难以确定色光与对样,影响织物符样,易产生原样色差。
染液配制
染液配制由称料、研磨、化料组成,其中配制染液时称料、化料的准确性,以及磨料、化料操作的规范化对织物的原样色差、前后色差的影响是十分明显的。如设备误差,对称量设备仪器的使用误差,称料、磨料、化料时的操作误差,染料的回潮不一致所造成的误差,所拼染料力分不足,以及同一货单所用染料生产批号不一等,都会造成染色织物的色光变化和色差的产生。
在此需要强调的是染料的回潮吸湿问题。在生产管理过程中,这一因素往往被忽视。据有关资料介绍,粉状染料中的添加剂具有较强的吸湿性,当空气的相对湿度较高时,染料的吸湿现象非常严重。在实际生产中,若将这样的染料用于拼色,对染色织物的色光、色泽深度影响很大;同时由于染料绝对使用量相对减少,织物染色后易出现前后色差和色光不符现象。
工艺参数的波动
织物在浸轧染液过程中,由于染液中各染料对织物的直接性存在较大的差异,达到动态平衡后,其工作液中的染料浓度与初始浓度会相差很大。在实际生产中,织物浸轧染料之前,即初开车之前,常对染液增浓(悬浮体染液增浓10%)或根据染料(水溶液)以不同稀释系数对染液进行相应的稀释。但生产实际中,由于工艺参数不稳定,仍会造成染色布的色差。
轧色打底机是热溶染色机和显色皂洗机工艺条件及参数的波动,直接影响染色后织物的色差。如车速不稳定,将打乱染液的动态平衡,造成织物染色后色光变化,产生前后色差。织物在打底机轧色过程中,均匀轧车的气压、油压的变化与波动,会造成染色织物左中右轧余率不一致,从而造成被染织物的左中右色差,严重时还会使被染织物产生明显的前后色差。另外,红外线及热风烘燥室温度、风量不均匀,如织物轧色后急烘会引起泳移,导致织物产生左中右色差或布面不匀。
还原蒸箱、皂蒸箱、水洗箱的温度,还原液、氧化液以及活性染料汽固时固色剂等工艺参数的不稳定或超范围的较大波动,都会对染色布的色光和染色牢度产生严重影响。还原染料皂洗不充分,会影响染料的正常发色。如还原黄G、灰BG、灰M、棕BR、蓝VB、紫2R等十几种染料在染中深色时会皂煮变色,而橄榄绿B却要加强皂煮才能正常发色。另外,活性染料染色后皂煮是否及时,也会影响其固色率。
3、后整理
后整理工序对织物色光的影响也非常明显。如染色织物经轧光整理后,织物的色光、深浅会有较大的变化;经涂层整理后,织物的色光、艳度变化明显。另外,在后整理拉幅过程中温度对热敏染料的影响也是十分明显的。即使进行一般的柔软、防水、硬挺等整理,染色布的色光也会受到不同程度的影响,严重时还会造成染色织物的原样色差,甚至左中右色差等。
染色布色差的预防与控制
实际生产中,在加强管理和强化操作的基础上,通过对织物染色时产生色差的各个因素进行分析,总结出以下预防和控制措施。
1、原样色差的预防与控制
染色织物原样色差主要是三方面因素造成的:由打样拼色染料选择不合理,生产机台染色处方调整不当,织物染色过程中工艺条件及参数波动较大。
合理选择拼色染料
打小样时,处方中的染料种类应尽量少。由于不同染料上染性能不同,减少染料种类可以减少染料之间的相互干扰。处方中选用的染料色相要尽可能接近原样,并且要尽量选择具有相似上染性能和上染曲线较一致的染料。
另外需要强调的是,仿样的染料与车间使用的染料在力分和色相上应尽量保持一致。由于同一染料不同厂家不同批次的产品,在色相和力分上存在有差异,应注意染料使用上的统一性,特别是拼色染料和调色光的染料,否则会对织物色光产生影响。如还原灰BG、灰M等。因此,实际生产中要加强控制,做到仿样、放样、正常染色生产,选用的染料为同一厂家同一批号,以避免因染料选用不当而产生色差。
根据染料特性合理修正处方
仿样和放样生产调整处方时,要注意染料上染性能对染色过程中色光的影响。如果所拼染料亲和力或上染速率有较大的差异,染色时就会出现初开车时产品色光符样,一段时间后色光发生变化的现象,即所谓色光逐渐减弱的现象。另外要注意染料的热变色性能的干扰,如前所述,一般绿色染料受热时偏蓝光,冷时偏黄光。因此仿样、大车试样和正常染色生产修正染色处方时,应根据染料的扩散性、亲和力、上染速率等性能,对染液进行合理追加或冲淡。同时对于热变性染料要等被染织物冷却之后再判断色光,进而对工作处方进行修正,以避免受染料热变性的影响与干扰。
此外,必须对染色过程中的工艺条件和参数进行严格控制,实施工艺条件及参数标准化,以有效地控制色差。
强化机台仿样、放样管理
由于化验室的染色条件与生产车间机台实际染色条件存在较大的差异,因此,正常染色处方要进行如下顺序的修正:小样处方修正→大车试样处方修正→正常染色处方修正,之后才能实施正常的染色生产。
在整个染色处方修改过程中,要加强管理,强化技术跟踪,掌握大车放样情况。化验室仿小样和正常染色生产时要按照规定的工艺条件及参数,不能以改变工艺参数来调整色光;大车试样的工艺条件及参数要与正常染色生产一致。
2、前后色差的预防与控制
染整加工过程中,染色织物的前后色差主要受配料、化料、半成品质量、工艺条件,以及参数的波动、设备机械性能这几方面因素的影响,所以预防和控制织物染色的前后色差,就主要从以下几个方面加强管理与实施控制:
严格控制半成品质量
织物前处理效果好,退煮漂做到匀、净、透,毛效、白度一致,丝光足,pH值稳定在6.5~7,这是织物染色成功的根本所在。必须强调的是,染同一色泽的织物,要用相同的前处理工艺,并尽量选用同一厂家坯布。另外,染浅色、鲜艳色时,需要选择白度一致的染坯,因为染坯的白度决定了染色成品的色光。
染液配制标准化
称料前要检查衡器是否准确;称料时按照生产工艺处方准确称料;称料后要把余下的染料桶盖好、封好,以防止染料吸收空气中的水分,影响染料净值。特别是调色光的染料,应根据所需用量将染料一次性称出研磨,然后再均分使用。另外,化料操作方法的统一化、标准化,都是解决织物染色布前后色差有效的预防和控制手段。
加强生产现场与操作管理
半成品的含湿量对织物染色生产的影响是相当明显的,必须强化对染前半成品的管理。生产车间可根据货单情况以及生产进度,控制好半成品的存量,对半成品实施封盖管理,确保半成品的湿度保持上下一致或在一定的范围内,以避免织物染色时产生前后色差。另外,生产工艺及参数的波动也会造成织物染色时出现前后色差。因此,加强生产现场与操作管理,是解决与预防织物染色布前后色差的有效手段之一。
3、染色布左中右色差的预防与控制
染色织物在连续轧染生产过程中产生左中右色差的主要因素有:半成品毛效、白度、布面含浆量、布面pH值等左中右不一致,均匀轧车压力,织物在预烘箱内所受的热处理,活性染料焙烘、热溶染色和补充染化液不当等。因此,要从以下几个方面采取预防和控制措施。
半成品质量的控制
加强前处理半成品的管理,尤其强调半成品效果与质量的一致性,也就是布面要匀。否则,会造成染色织物的左中右色差,而且这种色差在染色时较难控制与解决。另外,需特殊染整加工的织物的半成品质量更要严格控制。例如,磨毛产品的染整加工中,若半成品磨毛不匀或左中右毛效不一致,织物染色后就会产生左中右色差。因此,实际生产中强化织物的前处理,为染整加工提供合格的半成品是关键。
均匀轧车工艺及参数的控制
打底机是织物染色加工过程中的关键机台之一,必须保证均匀轧车状态完好,要保持均匀轧车左中右压力一致。生产中应做好如下工作:定期检查与测试油压、气压状况是否正常;定期校对仪表的准确性;定期检查轧辊的磨损情况;同时要求机台人员不准随意调节轧车油压、气压的压力或通过调节轧车压力的工艺参数来调整织物色泽的深浅。以上措施要做到定人、定责,严格控制,以避免织物在轧液过程中产生左中右色差。
织物受热的控制
织物浸轧染液后预烘或焙烘固色,应使织物在纬向上得到的热风量保持一致。织物浸轧染液后,在轧车压力的作用下将染料均匀地浸轧在织物上,若织物受热不一致,在烘干过程中染料就会产生泳移,使织物产生左中右色差,尤其是稀薄织物或涤类薄织物表现更明显。一般采取如下措施解决这类色差:定期检查循环风机的传动系统,确保循环风机左右风压一致;换品种刷车时要及时清扫左右加热片的防尘网板,确保防尘网板清洁,以免影响左右循环风机风量大小。
另外,涤棉混纺织物在高温热溶染色过程中,热熔箱内边中温度差异也会造成织物的边中色差。热溶染色机在空车情况下,热风嘴向内均匀喷风,不论是预烘箱还是热溶箱,一般总是中间温度高于两边温度。其原因是,箱体两壁和导辊两端在空气中有散热现象。而当染色打底机正常运转时,由于进预烘箱的是湿布,耗热大,两边热风交换快,织物易干,因此,整个箱体的温度就会变成为两边高中间低。而热溶染色机所进的是干布,焙烘箱的温度情况则与之相反,干布耗热较少,所以整个箱体的温度仍保持中间温度高于两边温度,有的设备由于对称度不够,或进布偏度较大,还会出现左中右色差。
热溶箱内存在左中右温度差异,就会导致布面上分散染料或活性染料的固色率和升华程度不一致。如织物含杂量较多或带碱量大,还会出现左中右泛黄程度不一,导致单色品种出现色差;多色品种若各染料的热敏感性不一,织物也会出现左中右色相不一。因此,只有彻底消除箱内温差才能解决色差问题。
在工艺上,可选用热溶曲线平坦的染料,因为在相同的染色加工条件下,染料性能不同,呈现的边中色差或左中右色差形态是不同的。例如,分散红3B染色后常会出现边深中浅色差;而用福隆大红S-BWFL染色,却常出现边浅中深色差。这是因为分散红3B系低温型分散染料,福隆大红S-BWFL系高温型分散染料。低温型分散染料在较低温度下即能固色,而高温则会造成染料的升华,影响染料的固色,造成边中色差的产生。高温型分散染料固色需要较高的温度,达不到应有的温度就会影响染料固着,得色较浅,所以高温型分散染料染色常出现边浅中深色差。
由焙烘温度不一致引起的色差,一般高温型分散染料较低温型分散染料明显,这主要是由于前者的热溶固色曲线大多不是很平坦,对温度较为敏感。
生产时产品的幅宽应低于风嘴的宽度,使焙烘室两侧有充分的空间,供热风在焙烘室内有较多的回旋和混合的余地。另外,设备上可安装活动阀门,对中间进风量进行调节;或者封堵风嘴中间约60cm,以降低中间温度。通过以上这些措施,可以有效地解决织物的左中右色差。
4、正反面色差的预防与控制
正反面色差在平纹织物染色时表现比较明显。产生正反色差的主要原因是织物在染整加工过程中,正反面受热不一致,一般是在烘干过程中染料产生泳移或染料固色所致。因此要解决这类色差,可以在打底机上安装红外线预烘装置,检查预烘室内风嘴离布面的距离,控制预烘室风机风量。
色差是织物染整加工中经常产生的质量问题,需要经长期不断地根据不同情况,采取相应措施。由于色差是在生产加工过程中产生的,因此,应综合分析各因素,结合生产现场情况制定有效的预防和控制措施,才能取得较好的效果。
关键字:染整色差,技术分析,色差的主要因素,染色布色差,预防与控制,面料
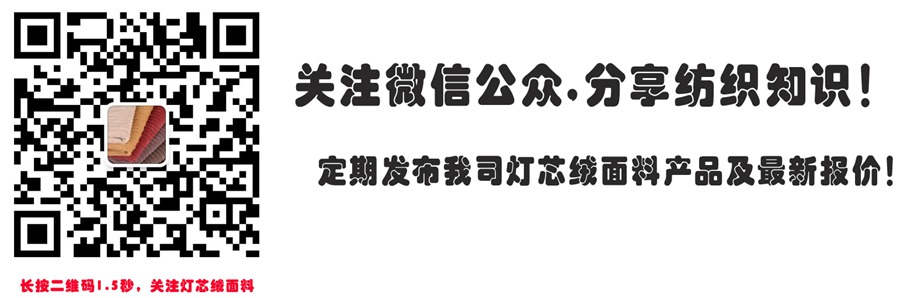
上一篇: 七月淡季,灯芯绒面料烧毛坯现货打折出售
下一篇: 氨纶的染色性能
![]() |
![]() |
![]() |
![]() |
![]() |
![]() |
![]() |
![]() |
![]() |
![]() |
![]() |
![]() |